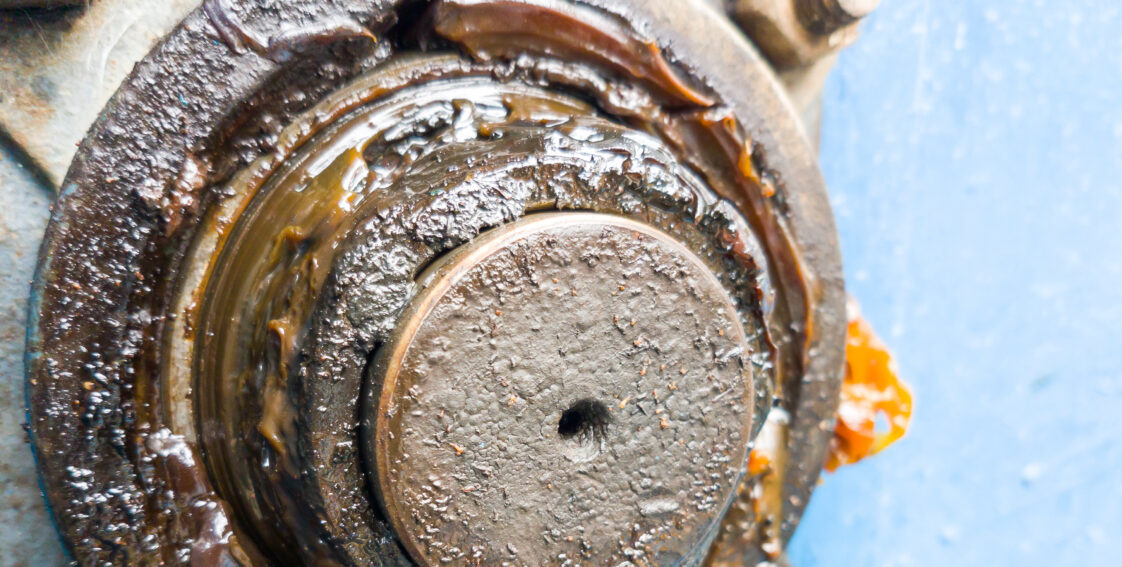
Without lubricant, friction will occur between moving parts, increasing wear. This is why it’s vital to add oil or grease to bearings, gearboxes, and similar rotating and sliding machinery.
Lubrication is probably the most important preventive maintenance action we take, yet it is possible to do too much or use the wrong type of lubricant. Over-lubrication issues may not be as serious as lack of lubrication. However, they can still increase friction and wear, raising operating costs, leading to breakdowns, and shortening equipment life.
Signs of Over-Lubrication

Over-lubrication is more common with grease than oil. This is because grease (which is oil plus a thickener) is engineered to stay in place around bearings and other moving parts while oil flows over and around them. With that being said, it is possible to overfill oil systems, which can also cause serious problems.
If you’re concerned about the possibility of over-lubrication, here’s what to look for:
- High back pressure or resistance when pumping grease into a joint or bearing.
- Excess grease around the fitting.
- Grease oozing out from the bearing.
- Grease pushing past a seal.
- Grease coming out of exhaust ports.
- In an oil lubrication system, foaming and knocking or other abnormal noises due to cavitation in the pump.
- Oil or grease on the floor under the machine or lubricated element.
Over-lubrication increases drag and friction, which generates heat. For grease, this can lead to the separation of oil and thickener, letting the lubricant flow out. When this happens, the protective lubricant film is lost, and metal surfaces can come into direct contact. If over-lubrication is suspected, it should be addressed quickly.
Causes
Over-lubrication happens in two ways:
- It can mean too much oil or grease is put into the bearing, joint, or tank.
- It can also mean lubrication is done more often than needed.
Over-lubrication results from the best of intentions. As a lack of lubrication is very damaging, people want to make sure to avoid it. The main reasons for doing it too often or applying too much are:
- There is no set schedule for lubrication.
- The lubrication frequency is set too high.
- No monitoring systems are in place.
- Too much grease is being pushed in.
- The grease guns are not calibrated.
- The exhaust port is blocked, so any grease that is oozing out isn’t visible.
- No level sensors or sight glasses on oil tanks.
Less often, hardware design can lead to over-lubrication. Grease might escape the joint or bearing in a way that isn’t visible (often resulting in an unpleasant and unsafe build-up on the floor). Or, there might be more grease fittings than needed, with the technician applying grease through each one.
How to Fix Over-Lubrication
If it is thought that a joint or bearing has been over-lubricated, the problem should be addressed as quickly as possible—delaying allows more time for heat to build up and wear to occur.
To fix over-lubrication:
- Remove all excess lubricant by wiping off any grease or lowering the level in an oil reservoir or tank. Note that there may be dry or crusty grease around the fittings that could get into the lubricated component. Be sure to remove any dried or crusted grease.
- Clean around joints, bearings, and fittings so you can see when any excess grease appears.
- If the unit being lubricated has exhaust ports, ensure these are clear so excess grease can flow out.
- Check for contamination and seal damage. Replace grease and seals as needed.
- Check for raised temperatures and/or vibration. Either could indicate damage that requires component or assembly replacement.
Preventing Over-Lubrication

Preventing over-lubrication issues is like dealing with any other preventative maintenance action: define what’s needed, establish a schedule and responsibility, and record when the work was done.
Specific to lubrication issues and greased joints and bearings, in particular, points to address are:
- Determine optimal frequency (usually from the manufacturer’s documentation) and the quantity of lubricant required.
- Document what lubrication is needed and where the fittings are, and log each time it’s done.
- Create preventative maintenance schedules for lubrication.
- Calibrate grease guns so the quantity dispensed per pump is known.
- Educate employees responsible for lubrication about the importance of following the procedure and the dangers of over-lubricating.
- Implement sensors to indicate when lubrication is needed (vibration monitoring is one approach, as well as using ultrasound to measure friction).
- Adjust lubrication frequency based on feedback from sensors and manual examination of bearing or joint condition.
Businesses may also want to consider installing automatic lubrication systems. These dispense a defined quantity at the designated frequency, or systems with built-in intelligence may dispense lubricant when needed, as determined by instrumentation on the equipment.
Get More Tips From DropsA
DropsA is a trusted manufacturer and engineer of automatic lubrication systems, including oil, air/oil, and oil recirculation. Please visit our blog for more tips and advice, or contact us today to learn how our systems can help you prevent over- and under-lubrication.