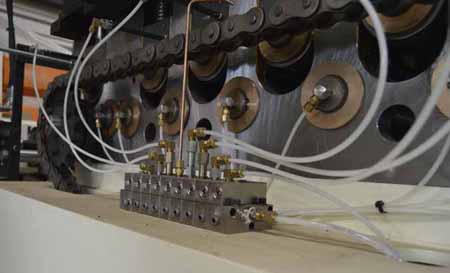
Lubrication is essential to the reliability, performance, and longevity of machinery. In the past, industrial equipment required manual lubricant application in key areas to prevent grinding keys, overheating cutting tools, and a wide variety of other issues specific to their application.
However, these days, automatic lubricators are one of the best ways to reduce wear and tear, lower energy consumption, and decrease costs associated with maintenance and repairs.
An automatic lubrication system, sometimes referred to as a centralized lubrication system, effectively lubricates various points of a machine and is controlled by a centralized unit or pump mounted in a location easily accessible by the operator.
Benefits of Automatic Systems
Automatic lubrication systems primarily help reduce wear and tear of device components, reduce energy consumption, decrease the amount of heat generated in machinery, and eliminate corrosion damage. However, when compared to manual lubrication, automatic systems offer even more benefits, including:
- Better Efficiency: Unlike a manual grease gun or oil applicator, automatic systems offer timed, measured amounts of lubricant to a specific point. The centralized controller will deliver timed, measured amounts of oil, grease, or other fluid, allowing you to add the lubricant in small amounts in short intervals rather than having to apply more lubricant than necessary to reduce the relubrication interval.
- Increased Productivity: There is no need to stop the machine to apply lubricant. Instead, these systems can lubricate components safely and consistently while your production line is in use. There is also a minimized chance of human error or danger when lubricating hard-to-reach lube points in the machinery.
- Increased Equipment Lifespan: Gears, cutting tools, and other friction points can all last for far longer if they are continuously and properly lubricated. By avoiding improper lubrication techniques, you can increase the lifespan of your equipment and prevent sudden breakdowns from stalling your line.
- Improved Worker Safety: Some lubrication points are dangerously close to moving parts. In the past, a worker had to move carefully to this position and apply the correct amount of lubrication. An automatic system prevents that dangerous maintenance step.
- Reduced Costs: Automatic lubricators use far less lubricant than typical manual application. Over time, you can expect to save a significant amount as your lubricant usage drops.
Common Applications
Automatic lubrication systems are used in many industries, including manufacturing, construction/demolition, semi-trucks, wind energy, mining, food processing, and waste processing. Any equipment requiring frequent lubricant application can benefit from an automatic system.
When to Use Automatic Systems Over Manual

Nearly all manufacturers benefit from automatic lubrication systems, especially if constant lubrication is needed, such as in production lines used for hours at a time. The constant motion of the press and the constant punches and shearing all cause frictional heat, which can damage parts if the heat isn’t checked beforehand. Automatic systems are also great for lubricating hard-to-reach machinery components.
Comparatively, manual lubrication is better for extremely small operations and components that are easy to reach or don’t require much lubrication. For example, if you’ve ever seen a metal die press up close, you’ll notice that on each corner of the press, there’s a long metal slide that facilitates the movement of the press. Die techs usually slather grease lubricant on these slides weekly to help keep the slide lubricated. This is a good example of when manual lubrication is preferred over automatic.
Common Components of an Automatic System
Lubricants
You can’t have an automatic lubrication system without lubricant. There are two primary types of lubricants: grease and oil.
Filters & Collectors
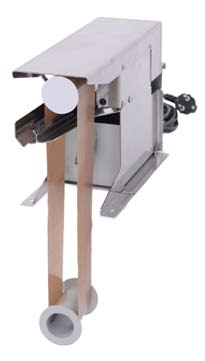
Even the best lubricants become contaminated by dust, debris, and other particles. Filters and collectors help prevent bearing damage by capturing that debris and dust.
Lubrication Pumps
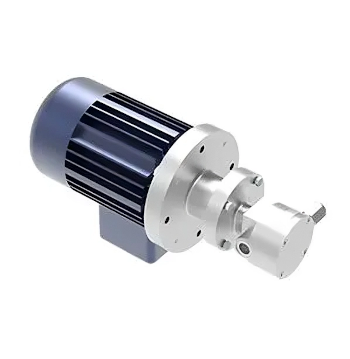
The entire system is powered by an electric, hydraulic, pneumatic, or mechanical pump. Automatic systems use a range of pump sizes and specifications, depending on the number of fittings and lines, as well as the type of lubricant used.
Reservoirs
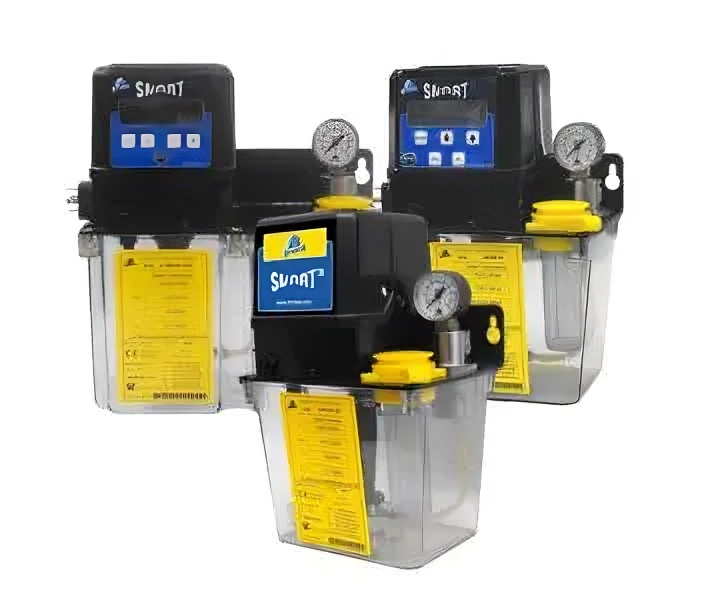
This component stores all of the lubricant that will be distributed to the various points.
Controllers

A controller sets the frequency and amount of lubricant application. State-of-the-art controllers, like the VIP5 Controller, even offer pulse, cycle, and flow features. Controllers usually feature a simple menu and easy-to-read screen to allow drivers to conveniently operate the systems from inside the cab.
Monitoring Systems
Various sensors and monitoring devices prevent automatic systems from over-supplying lubricant points or leaking grease or oil onto other areas of your equipment.
Lines

Lines (consisting of tubing and hoses) carry lubricant to specific points in machinery (called lubrication points).
Valves
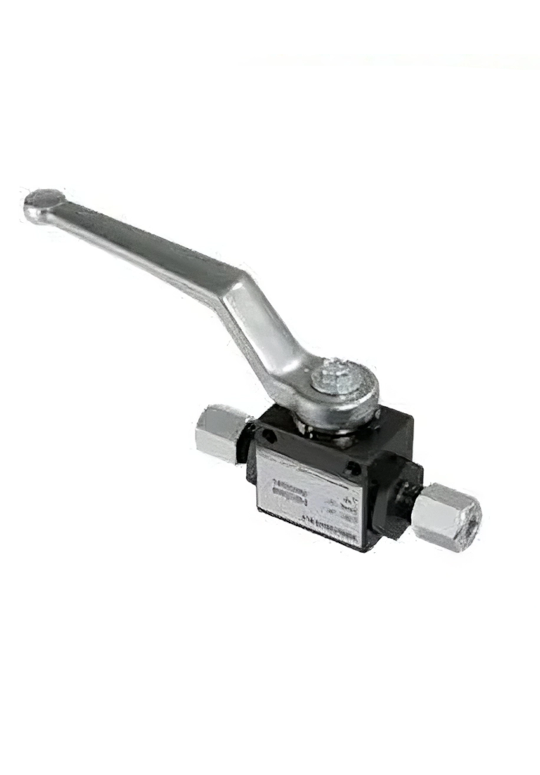
Valves (sometimes called metering devices) control the amount of lubricant at each point. There are two primary types: injectors, which deliver specific amounts of lubricant, and progressive valves, which deliver small amounts of lubricant at specific points.
Spray Nozzles

Similar to valves, spray nozzles are an optional system component. Nozzles come in different types and attachments and allow you to adjust the spray pattern. Patterns could include a blade-shaped, cone-shaped, flat spray, etc., for more targeted lubrication.
Types of Systems
Automatic systems can be categorized in two ways: 1) lubricant type and 2) lubrication method.
Lubricant Type
Grease Systems
This system type delivers grease to lubricate pins, bushings, gears, and other components from a centralized system. It can be used for vehicles and machinery, such as die presses.
Oil Recirculation

This automatic lubrication system keeps the oil in a continuous flow. It can ensure exact quantities, temperatures, and quality of the lubricant. It substantially reduces oil waste, meaning the system is less expensive and easier to maintain.
Air/Oil

This style of automatic lubricator applies a spray of air/oil mix. It is very compact and requires much less lubricant than other systems. It is a good fit for chain, gear, spindle, and vacuum pump lubrication.
Lubrication Method
MQL

Short for minimum quantity lubrication, an MQL system reduces the amount of lubrication needed by monitoring and strictly controlling applications. It is well-suited for machining and CNC applications.
Total Loss Lubrication
In this type of system, the lubricant isn’t recirculated. It’s used once and then used during operation. The direct advantage is that it reduces potential contamination, as the fluid, grease, or oil isn’t recirculated. It’s commonly used in two-stroke engines, machinery in harsh environments, and railway systems.
Single-Line Progressive
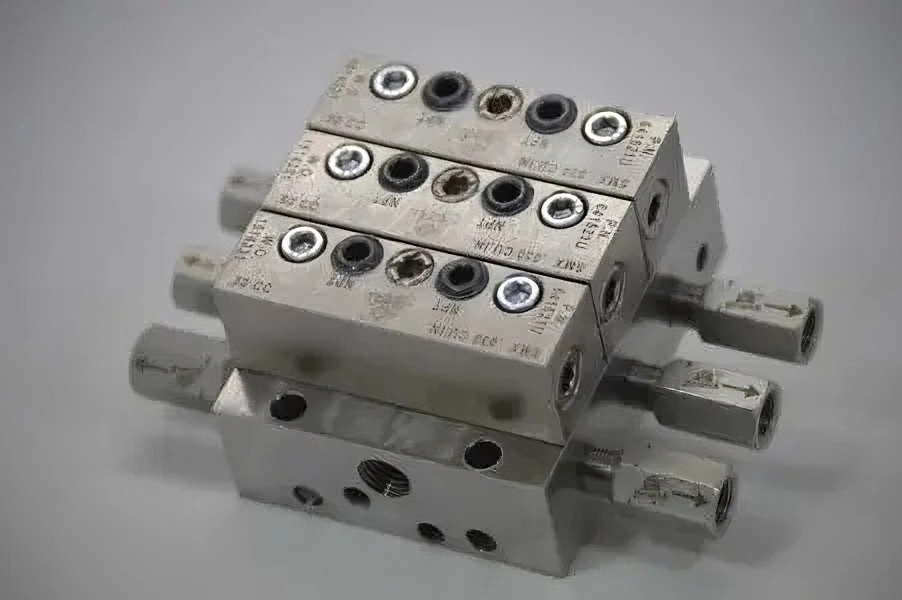
This simple setup features a single line that pumps the lubricant to the needed area. There are various reservoirs and pumps throughout the system. “Progressive” systems feature specialized valves (called dividers) that allow you to divide the lubricant flow into smaller, precise amounts at each point. They’re primarily used in automated production lines, construction equipment, wind turbines, and injection molding machines.
Single-Line Parallel

In this design, the system uses a single main line to supply lubricant to multiple lubrication points. The lubricant is pumped through the main line and distributed to each point with metering devices (sometimes called injectors). The lubricant is distributed “in parallel,” which means that each point receives lubricant at the same time and independently, ensuring failure at one point doesn’t affect other points. Common applications for this design include conveyors, presses, printing machines, and textile machinery.
Single-Point
A single-point system only delivers lubricant to one specific point. They are self-contained, easy to install, and commonly used to provide constant lubrication to bearings, chains in conveyor systems, motor bearings, and small, enclosed gears.
Dual-Line Parallel
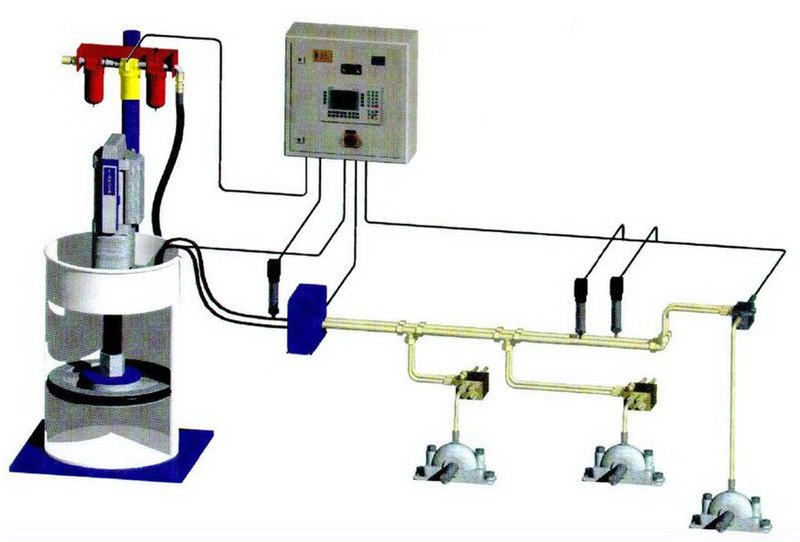
This setup uses hydraulic pressure to power the metering valves and distribute specified amounts of lubricant. There are two lines alternating between acting as pressure lines and vents. The benefit of this is that a single pump station can deliver lubrication to many parts spread over thousands of feet of tubing. This design can be great for high-load applications and large machinery like rolling mills.
Multi-Line
Multi-line systems have a series of pumps that help lubricate parts in machines or on a progressive die line. They have multiple points within the line that distribute lubricant. Each point operates independently. They’re commonly used to lubricate critical and high-value robotic equipment and marine engines.
How to Choose a Lubrication System
Choosing a lubrication system can be tricky and time-consuming, as there are numerous factors to consider, including:
- Parts or Equipment That Needs Lubricated: You have to factor in all the parts of the production line and what their roles are within the production process. List each part’s failure points or thresholds in order of importance to figure out which ones should get the most lubrication. Also, consider the size of the equipment or component, which can help you understand how many lubrication points you’ll need.
- Operating Environment: Will the system be exposed to dust, moisture, and/or extreme temperatures? If so, your system will need to be able to withstand these conditions.
- Type of Lubricant Needed: The system you choose should be able to handle the specific viscosity of the lubricant you need to use.
- Variability & Customization: Do you need to adjust the flow rate? If so, you may want a progressive system or one with control valves.
Learn More From DropsA
DropsA is an industry-leading supplier of automatic lubrication systems and high-quality components, including nozzles, pumps, and controllers. We help manufacturers in many industries, from marine, aerospace, and defense to food and beverage, find the right lubrication solution for their applications.
Please visit our blog for more resources or contact us today to get help finding the right system.